GARO securing the power supply at Micropower Group’s newly built production plant
With the construction of a climate-smart production plant in Växjö, Sweden, Micropower Group has gathered all its operations under one roof. GARO was entrusted with delivering products and custom solutions for an effective power supply for the 25,000-square-metre plant. The newbuild brings together the company’s head office, production facilities and research and development centre.
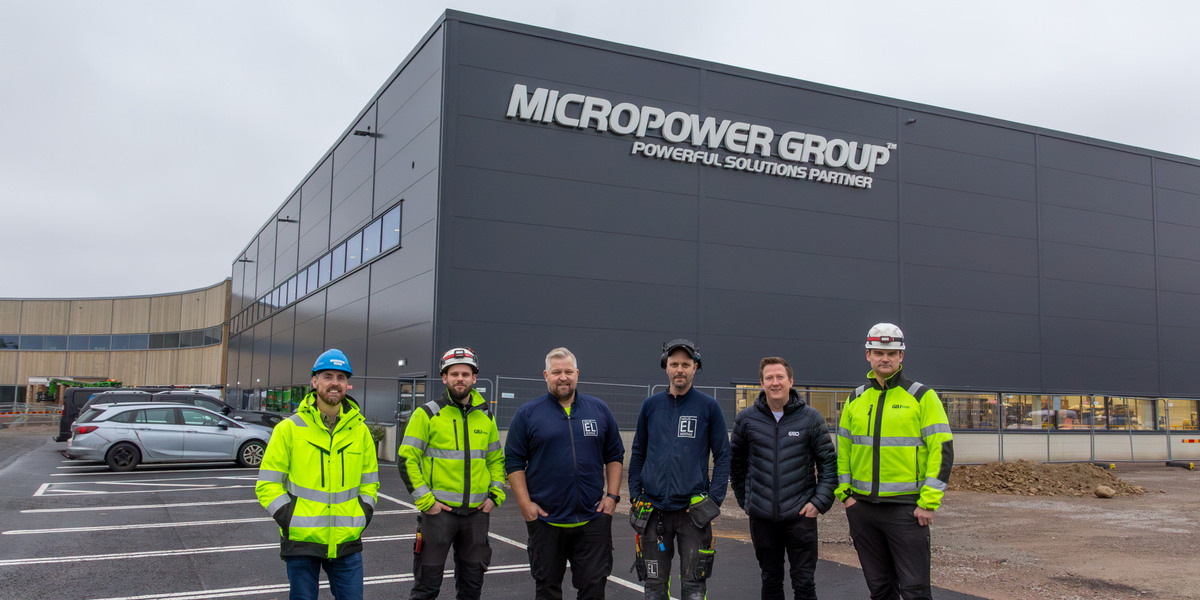
The turnkey contractor for the construction project is GBJ Bygg, which together with carefully selected suppliers and subcontractors has ensured steady progress. One of the companies involved in the construction project is Växjö Elmontage, which considered the supplier for the power supply a given.
“GARO is both flexible and dependable. A supplier with extensive experience that understands our needs and delivers custom solutions quickly and conveniently. In a larger project such as this, it’s important to collaborate with a stable and responsible partner such as GARO. We’ve been collaborating with GARO for over 25 years and know that we can always rely on them. A reliance that offers peace of mind at all stages of the project,” says Henrik Hammarström, Project Manager at Växjö Elmontage.
GARO’s role in the project, in close concert with Växjö Elmontage, has been to deliver tailored power supply solutions, including switchgear, distribution cabinets, cable cabinets and outlet boxes. The project is perfectly aligned with GARO’s core expertise, combining the company’s knowledge of power supplies with a focus on sustainability and innovative products and solutions.
“We’re proud of the confidence shown in us and consider it testament to our expertise in the field of power supplies. This project also demonstrates how fruitful collaboration between all involved helps ensure a smooth and efficient work flow,” says Daniel Emilsson, Business Area Manager at GARO Electrification.
Linus Nilsson, Sales Manager at GARO Montage, the company’s assembly wing, has been actively involved in the project and highlights the fact that Micropower Group’s ambition to build a climate-smart plant is in line with GARO’s focus on developing products and solutions with the lowest possible environmental impact.
“In this project, we’ve also had very short transport distances – from sheet metal forming in Gnosjö to finished products in Hillerstorp, where assembly takes place before final delivery to Växjö,” he says, continuing:
“That’s a total transport distance of just 100–150 km, and that small stretch of road transport helps ensure both lower environmental impact and extremely fast delivery times.”
Read a long version of the article here.